3D printing brings efficiency, educational opportunities to the precast industry
Evolving technologies provide companies and businesses with opportunities to improve their products and techniques. But what if there was a way to preview physical products before they are even created?
Thanks to 3D printing, there is.
3D printing is a manufacturing process that allows the user to create a three-dimensional object from a digital file, which can then be used for a variety of different design improvements and even educational purposes.
Precast concrete plants are discovering the efficiency of this technology and how to best use it as an engineering tool.
THE SOLUTION BEFORE THE PROBLEM
In 2019, Garden State Precast’s president was pushing for the company to follow his vision and start incorporating 3D printing into their projects.
“His vision worked out really well, and we are still using [3D printing] to this day,” said Robert Romanow, the director of engineering and compliance at Garden State Precast. “We don’t use it for every little project but anything that is out of the ordinary or a little more complex we do.”
Romanow said Garden State uses 3D printing mainly for specialty items before they head to the production floor and to make some promotional items for clients.
They now have two 3D printers, which cuts production time in half, according to Romanow, and even finds solutions before problems occur.
“We’ve realized that a drawing that we had submitted and had been approved by however many different people had a post tensioning tube that overlapped with the pipe opening,” Romanow said. “So, from there we were able to evaluate the move of the post tensioning tub, and, if they didn’t notice that during the model, then we wouldn’t have noticed it until in actual production and that would’ve been a problem.”
Gainey’s also utilizes 3D printing in hopes of troubleshooting before they break ground on a project.
“We can print this model and use a printer and bring it to the engineering firm and then they can kind of start troubleshooting, OK this will work or this won’t,” said Cyndi Glascock, senior design manager at Gainey’s. “You can have a better and real-time conversation about how to troubleshoot and build a better mousetrap on some of these designs, how to improve the design and what we can do differently.”
They focus on using their 3D printer for more unique items they feel people are struggling to get their heads around visually.
Some precast companies, such as S&M Precast, have even used their 3D printer during production.
S&M wanted a plastic component that they couldn’t buy, so they ended up creating one themselves with the help of their 3D printer.
“We wanted to create a little piece of plastic that we put into concrete, and it holds a block of wood with a screw on the top of it,” said Ray Graf, vice president of S&M. “It hooks the block of wood to the concrete so that we can pick the concrete up with the forks. This prototype is still in production daily.”
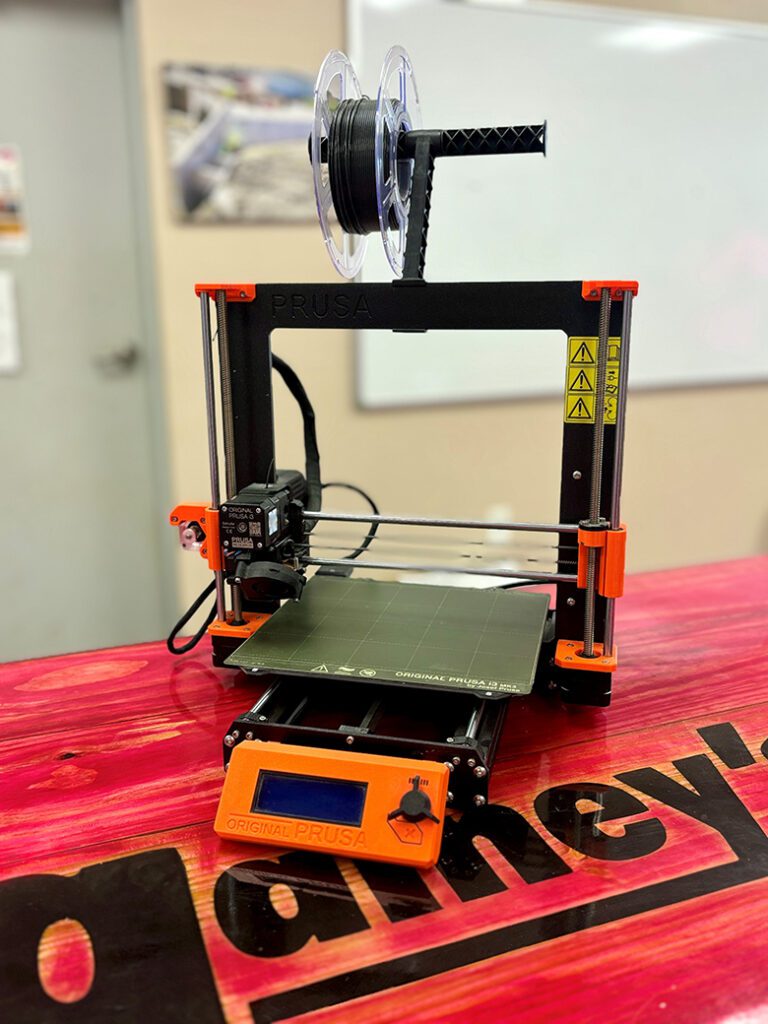
A LEARNING OPPORTUNITY
Gainey’s started using 3D printing a few years ago to model their products, especially newer ones, and often takes the printed models to schools or trade shows to demonstrate how their structures work and fit together.
Glascock has noticed students and engineers enjoy having a tangible item.
“They kind of even almost feel like it’s a toy,” Glascock said. “A lot of people are visual learners and they’re going to want to touch and see and that kind of thing.”
One of the models that Gainey’s has printed was a bridge with all the different components that have to be pieced together to build the final product. Glascock said having students or even engineers hold the model will help them understand how the pieces fit together.
“We will print the components as if they’re concrete pieces and then show how the whole bridge and how it will fit together for the application that is needed,” Glascock said.
Showing a physical product, even in miniature, to students or engineers helps them better understand the final product.
“We’ve recently started doing this product line that is elevated precast platforms,” Glascock said. “We have so many times that we have to elevate structures like generators or control buildings and these precast platforms allow [elevation] versus the metal that you’re used to. So, we printed these precast platforms to show how it all shifts in one piece and then just set the slabs on.”
Romanow agrees that having a miniature model of a project helps production workers before they begin production.
“The production workers will have something they can look at and hold and see what they’re going to be building beforehand, which is more of a benefit then just looking at a piece of paper with some dimensions and line work,” Romanow said.
THE FUTURE OF PRINTING PRECAST
With the precast concrete industry growing, companies are always looking for more efficient ways to keep the quality of their products high up while keeping their problems low.
3D printing is becoming a more mainstream solution with its low cost and efficiency compared to other systems.
“I foresee more companies turning toward 3D in general whether or not they are going to print,” Glascock said. “But for precast companies, I do think it is a good thing to adopt.”
Glascock said 3D printing is the way to go when it comes to showing how components will or will not go together.
Romanow agrees that 3D printing will be seen throughout the precast industry within the next couple of years.
“I think as it become more readily available, the prices are going down and it’s not as expensive as it was years and years ago,” Romanow said. “My kids are even learning [3D printing] in middle school so it’s going to be wherever it needs to be; in a few years it’s going to be more commonplace for sure.”
On the other hand, Graf believes there will be a day when 3D models come to life.
“I really think there will be a day when we 3D print concrete structures,” Graf said. “Technology just needs to move along and that’s where it is headed.”
We may already be there.
A concrete company is nearing completion on a completely 3D-printed neighborhood in Georgetown, Texas, with a printer that is more than 45 feet wide and weighs 4.75 tons.
The future of printing precast, whether small or big, is not as far off as one may think. Along with new generations and evolving technology, the future of precast as we know it is changing every day.