Culture key in reducing labor-related toll on body
Labor, manual or otherwise, takes a toll. Whether it’s craning your neck and slouching your back over a computer keyboard or straining your legs and back to haul loads across a warehouse, the work that we do has an arduous effect.
No precast or other manufacturing expert needs to be told this, but it’s worth repeating – a production plant presents a significant set of physical challenges and strenuous movements. According to the Occupational Safety and Health Administration (OSHA), one in 10 manufacturing workers is injured annually. Much can be done to adequately protect and enable workers to perform as effectively as possible.
Many precast plants already are taking steps to do so.
“I think there’s a great culture … every facility I’ve been to has an excellent safety culture,” said Michael McKinley, co-founder and director of operations for exoskeleton manufacturer SuitX. “It’s ingrained from the beginning.”
So, what injuries are most commonplace? Given the nature of precast work, wear and tear occurs from a cumulation of stress put on the body over time. Stress from bending over or kneeling to manually bolt, tie or generally manipulate parts of a structure is largely unavoidable, particularly in the case of large precast structures.
“I think whenever possible, we try to engineer the problem out of the job,” McKinley said. “If we can, let’s get that individual in a posture that is eliminating the risk of injury. And most of the time within concrete or precast, that’s basically impossible to do, because a floor needs to be on the floor … The structure is just so enormous and so massive, there’s no good way to really improve that.”
Speaking to safety culture at large, it’s the most important step in protecting worker health. Not coincidentally, it’s also the most noticeable. Thorough signage indicating potential hazards is essential and effective. Machine guarding and maintenance helps prevent technological failures out of a worker’s control. Meticulous labeling of a component with warnings, the manufacturer and technical details (voltage, weight, dimensions) all reinforce a workplace’s commitment to safety and injury prevention.
To further that culture, one of the most comprehensive representations of hazard reduction in the workplace is the National Institute of Occupational Safety and Health’s (NIOSH) “Hierarchy of Controls.” These guidelines – while not a cure-all – can aid in focusing efforts to tangibly and noticeably ensure safety in the precast construction environment. Working down the hierarchy (attempting the first method before moving to the second, and so on) allows employers to exhaust every measure to best protect workers.
Elimination: Remove the hazard at the source. This is the most effective form of hazard defense, and, in this discussion, precast manufacturing thrives.
Automating processes when applicable and reliable also is vital and still relies on the expertise of a plant employee – just in a form that hopefully removes the degrative effects of hands-on component manipulation. Unfortunately, nothing eliminates the need for manual operation across the entire precast process. Smaller components still need hands, wires still need tied, and smaller 50- to 75-pound loads are still best served by human beings.
Substitution: Offer a safer alternative to the potential hazard. When considering injury prevention, the best substitute for frequent jarring movements and heavy lifting is lighter loads and easing those movements.
NIOSH notes that elimination and substitution can be the most challenging actions to integrate into an existing process. In a well-established setting like a precast plant, integrating substitutes is difficult, but keeping equipment updated is necessary.
Engineering Controls: Institute controls that reduce or prevent hazards from coming into contact with workers. The best engineering controls prevent workers from doing more than they must. Making user action minimally necessary for processes to occur – without reducing quality – further reduces workers’ bodily stress. Integrating it with already well-engineered technology makes an even bigger impact.
For example, use elevated casting tables or reinforcing jigs that hold an assembly off the ground.
“I’ve always been impressed by when you go to these plants, and it’s this amazing combination of ancient technology and super modern technology,” McKinley said. “We’ve been doing concrete since the Romans. We have this great environment of automation and human coming together… they’re symbiotic and they’re assisting each other.”
Administrative Controls: Establish workplace practices that diminish exposure to hazards. In regard to protecting workers’ bodies, this can be boiled down to treating workers’ bodies as any coach would treat an athlete. Every worker in a plant is an athlete in their own right, lifting objects and performing tasks that test the body over time.
Proper training in the different modalities of precast manufacturing is vital. Qualified employees training someone on how to best perform each aspect of the job is paramount in protecting workers from improperly operating equipment in ways that may hurt them. Job rotation also prevents workers from overexerting themselves by frequently transitioning between work to minimize pressure on different areas of the body. Finally, proper break time to ensure recovery from any form of labor is necessary – whether hauling rebar or sitting in a desk chair – your body appreciates it.
Personal Protective Equipment (PPE): PPE is simultaneously the final layer of preventative measures against hazards and one of the most proactive. Everything from gloves, earplugs and hard hats to wire guns and respirators is personally protective. While improving the work process is still the best prescription to injury prevention, implementing a comprehensive PPE program can be the cherry on top – just one extra means of protecting workers’ bodies. For example, waist back support belts can be used as PPE to avoid lifting-related injuries.
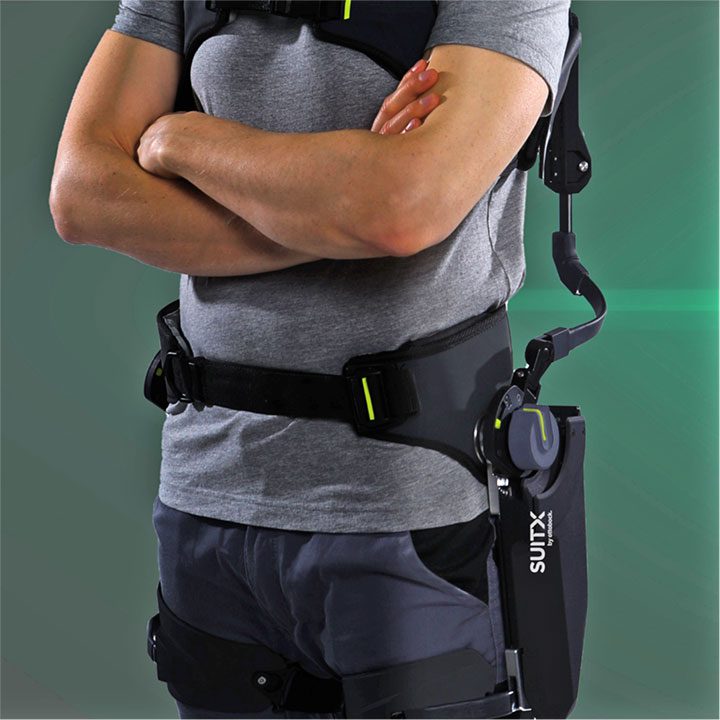
And PPE innovation has by no means stalled. McKinley’s company, SuitX, has multiple lines of wearable exoskeletons designed to ease the force imparted during manual labor. The technology has proven to help alleviate forces on joints and muscles from the shoulders down to the back and legs. Similar progress is a continuation of the efforts to elongate the healthy lives of all people who perform physically straining jobs, including in precast.
“Precast has a huge advantage in that you’re able to reuse the same form, same bed, day after day, strip it, build it again,” McKinley said. “And it’s much more of an efficient process from that perspective. You end up with specialized crews that are doing tasks – for example, wire tying – on a shift-long basis. So, in precast it just works really well. It’s a good niche for this kind of product, because you can see benefits immediately from reducing the risk of injury.”
Human bodies are the most remarkable feat of engineering we witness. Our ability to withstand the pressures of manual labor for years at a time remains astounding, but performing is better than merely withstanding. With a combination of preventative measures and a strong safety culture, precast workers can have an expectation to work hard and have their bodies protected, too.
“They’re innovating,” McKinley said. “These plants are innovating, and they’re moving forward in ways to improve these the health and safety of their entire environment.”