Solutions for removing snow and ice from precast concrete steps without deteriorating the product
Since the 1940s, precast concrete manufacturers have offered steps among their stable of products, though they have become more niche than mainstream over the years.
The benefits of precast concrete steps mirror that of other precast products. Namely, they are produced in a controlled environment of batching, mixing, casting and curing to provide the most uniform and highest quality concrete. They also get slippery when wet or frozen.
To combat those conditions, homeowners and commercial maintenance professionals turn to
de-icing materials, which present a series of issues on their own. De-icing chemicals potentially can lead to damaging concrete steps and reduced service life. Consequently, an overwhelming recommendation by the precast step producers nationally is to never use de-icing chemicals.
There is a dichotomy between precast concrete step producers’ recommended policy of not using de-icing chemicals and an awareness by those producers that people will use them regardless in wanting to make icy steps as safe and slip free as possible.
However, if both parties become fully educated on the specific de-icing issues and implement best practices under their control to mitigate the potential detrimental effects that chloride de-icing chemicals may have on precast concrete, it will make the world a safer place, one step at a time.
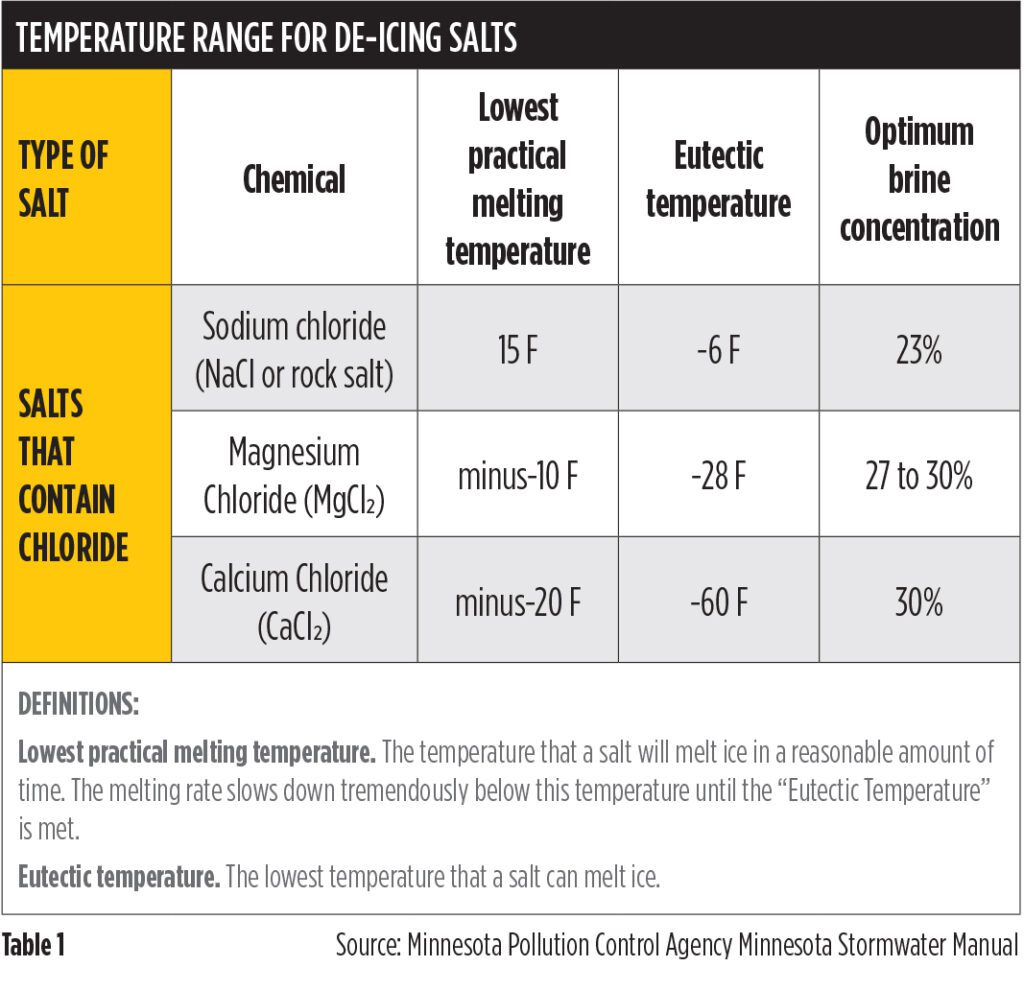
DE-ICING PRECAST CONCRETE
The application of de-icing products and salt help provide safe movement up and down steps by removing some of the slipperiness.
Chemicals in de-icing agents lower the freezing point of water and break the bond between ice and pavement. But while effective in reducing the ice hazard on concrete surface, some chemicals can affect durability.
The most common de-icing salts used by the general public include sodium chloride (NaCL or “rock salt”), calcium chloride (CaCl2) and magnesium chloride (MgCl2). All three come in bags or 5-gallon containers and typically are sold as crystalline or pellets.
Each product offers different attributes regarding the temperature range in which they work best. Each also has a different capacity to potentially harm concrete.
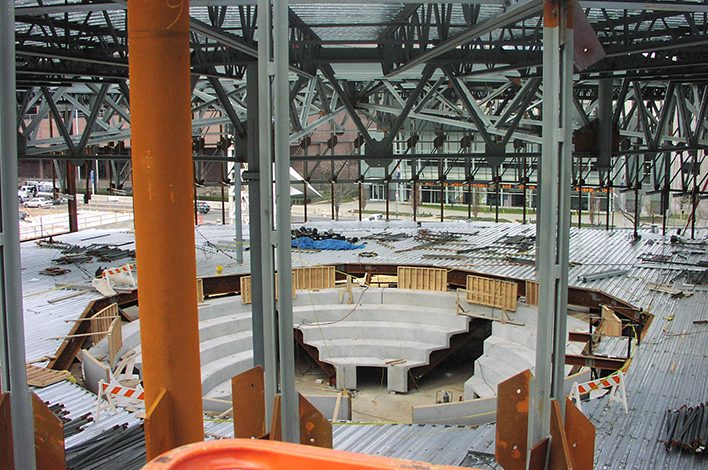
BUYER BEWARE, BUYER BE INFORMED
Studies on the effects of de-icing chemicals on precast concrete steps are few. The Environmental Protection Agency offers a “Safer Choice” designation for deicer products that fulfil certain criteria. However, there is no national standard nor labeling requirements for de-icer packaging.
Claims such as “environmentally friendly” or “pet friendly” very well could be pure marketing with no science to back it up. So be sure to do some research and make decisions accordingly based on ingredients and guidance.
There is plenty of research, however, on the effects de-icing products have on concrete roads and bridges. And while precast concrete steps are a much smaller scale than roadway systems, both have the same basic functionality – moving people safely from one location to another in slippery winter conditions.
Much of this research can be applied to de-icing strategies and practices for precast concrete steps. So it is OK to extrapolate a little.
Certain field conditions or contact with specific chemicals or acids cause what the Federal Highway Administration describes as material related destress (MRD). This condition is broken down into physical and chemical mechanisms.
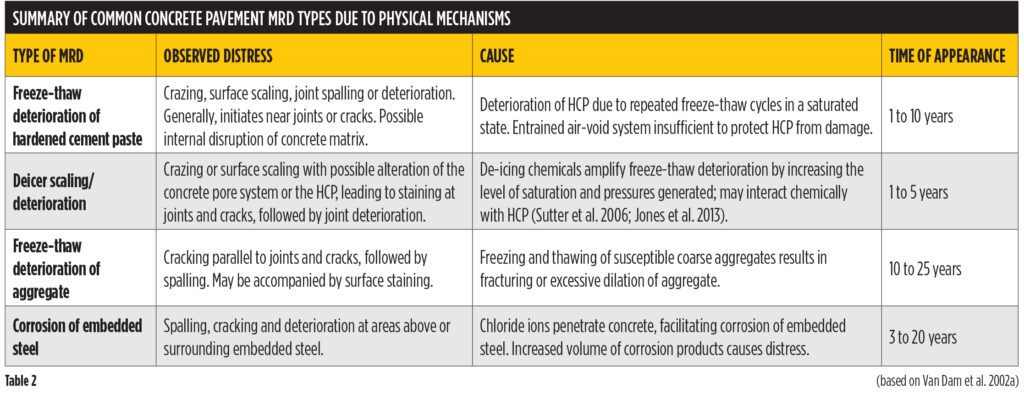
The mechanisms in Table 2 show specific FHWA-identified MRDs that are related to freeze-thaw damage and those based on the use of de-icing chemicals.
For more than a decade, a deleterious attack on concrete pavement joints has been identified and researched (Sutter, J. Weiss, Farnum, et al) due to the application of calcium chloride and magnesium chloride de-icing chemicals and the creation of calcium oxychloride. Concentrated applications of these same chemicals to precast concrete steps may also produce problematic expansive reaction through the creation of calcium oxychloride within the concrete matrix causing spalling and cracking.
Research has shown that the use of secondary cementitious materials (SCMs) – specifically fly ash, slag and silica fume – in the concrete mix reduces the calcium hydroxide available for problematic calcium oxychloride formation through dilution and pozzolanic reaction within SCMs. Consequently, this greatly reduces the potential of calcium oxychloride formation.
Another reason to utilize SCMs beyond improved concrete performance is they typically are good for the environment and increase profitability. However, fly ash’s availability is becoming limited with changing environmental and power policy.
With that in mind, a recent paper, “Mitigation Calcium Oxychloride Formation in Cementitious Paste Using Alternative Supplementary Cementitious Materials,” (Jones, Ramanathan, Suraneni, Hale), was published in March 2023 that prepared laboratory samples of concrete using traditional and alternative SCMs. The study compared each materials’ capacity to mitigate the formation of calcium oxychloride.
The rankings of most effective to least was as follows:
- Rice husk ash
- Type C fly ash
- Type F fly ash
- Bottom ash
- Nepheline syenite filler
- Silica flour
- Limestone filler
- Sandstone filler
Additional testing would be needed to verify the concrete characteristics with alternate SCMs meet or exceed the existing concrete characteristics utilizing traditional SCMs.
THE FUTURE OF CONCRETE ICE MELTING
A 2017 research collaboration between Drexel University, Purdue University and Oregon State University titled “Incorporating Phase Change Materials in Concrete Pavement to Melt Snow and Ice” has shown by that introducing phase change materials into a concrete mix can store energy, which can be released as heat when temperatures drop and material begins to solidify.
The phase change material utilized within this project was paraffin wax. Though promising, the technology remains preliminary with additional research required to determine the optimum phase change material and the effect it may have on fresh and hardened concrete properties along with durability considerations.
One potential future result is precast concrete steps where the approach is “no salt, no shovel, no ice.”

BEST PRACTICES FOR DE-ICING
There needs to be a balance between concrete step producers who advise against all deicers and peoples’ needs to scale the steps safely. Here are some approaches:
- Remove the snow. The best and simplest means to reduce the formation of slippery ice on steps – which over time can damage the concrete – is to remove the snow prior to ice formation as soon as possible by shovel or broom.
- Topical concrete sealant. Either during production or shortly after delivery and installation, apply a silane, siloxane or agriculturally based soy methyl ester polystyrene coating in accordance with manufacturers requirements on tread, rise and platform surfaces. This should be an ongoing maintenance item for durability. A simple test to determine if reapplication of a topical sealant is needed is to pour water onto a dry step. If water beads, it is OK. If it absorbs water, it is time to reseal. The frequency of reapplication can vary from three years to 10 years depending on step use and pedestrian usage volume.
- Temporary rubber covers. Place removable rubber covers over the step tread and platform, which can form a barrier between the step and ice. This can be lifted exposing a clean, safe, non-slippery surface.
- Utilize a traction material. In lieu of a de-icing salt spread, use an abrasive sand or native bird seed such as white millet or “no-mess” sunflower seeds.
Prior to using chloride chemical as a step de-icer:
- Know your steps. It is universally recommended that any precast or cast-in-place concrete not have de-icing agents applied within one year of the curing cycle completion. Utilize an abrasive, such as sand, for step and platform traction. The techniques described above should cover that first winter.
- Choose wisely. When using a chloride de-icing chemical, choose the correct chemical for the temperature conditions.
- Be wary. Claims within some deicer packaging of “safe” with respect to concrete, pets, plants and environment can be misleading or false. With respect to concrete durability, research has shown that sodium chloride (NaCl) on properly produced concrete is the least deleterious de-icing agent when compared to calcium chloride (CaCl) or magnesium chloride (MgCl).
- More is not better. Do not use a scoop-and-dump technique. Apply the de-icing chloride evenly and sparingly.
- Get ahead of the storm. If possible, place the de-icer appropriately prior to a storm event. If that can’t happen, shovel off the snow layer, then apply the salt.
- Remove the slush. After the de-icing chemical has done its job of creating a brine that will break the formed ice from the concrete step, it is important to remove the ice and slush slurry as soon as possible. This prohibits the slurry material from potentially providing critical degree of saturation of brine water into the concrete, effectively filling all the air entrainment void space and possibly creating cracking or scaling when the water refreezes within the concrete.
- Clean up. After the snow has cleared and steps have dried, clean up any large deposits of de-icing residue or clumps of de-icing salts that may have gathered during spreading or slush drainage. Wash down steps to clear off de-icing chemicals for when warm temperatures arrive.
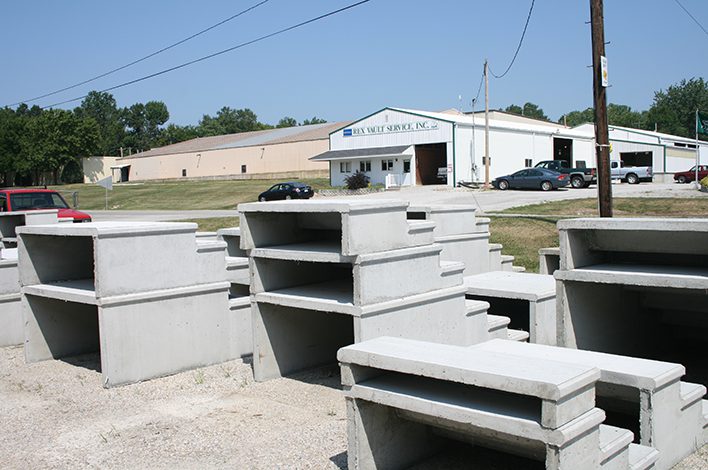
PRECAST PRODUCERS BEST PRACTICES
There also are steps that precast concrete step producers can take to help customers preserve the product. The simplest is adhering to the concrete mix and production requirements for optimum precast step durability when subjected to freeze-thaw conditions and potential de-icing chemical exposure.
Here are others:
- Water/cementitious ratio. Reinforced concrete containing ferrous metal reinforcement (rebar or fibers) should not exceed 0.4. Non-reinforced concrete should not exceed 0.45.
- Secondary cementitious materials. Utilize fly ash, silica flume or slag as cement replacement percentages between 15-30%. This improves the concrete matrix density with corresponding reduced water and chemical transport properties and mitigates potential for deleterious expansive calcium hydroxide formation when calcium chloride or magnesium chloride is utilized as a de-icing agent.
- Aggregates. Coarse aggregates should come from sources that have test confirmation to resist freeze-thaw (D-cracking) in accordance with local DOT agency experience and criteria.
- Air entrainment. For wet-cast concrete between 6-8%, test in accordance with ASTM C231, ASTM C173 or other recognized air-void testing methods such as utilizing the Super Air Meter apparatus per AASHTO T395. Production practices should provide air content verification to occur not less than for each 150 cubic yards (115 cubic meters) of concrete but not less often than once each day.
- Finishing. Exposed surfaces of treads and platforms should have screeds and trowels of wood or magnesium. All bleed water should be removed or allowed to evaporate prior to final troweling or broom finish. Finished surfaces of treads and platform should be checked by rigid straight edge or other devices to verify no small water ponding low spots.
- Curing. Curing methods should follow the guidelines established within the 2023 NPCA Quality Control Manual for Precast Plants Section 4.5 Curing Concrete.
PRODUCER VALUE ADDED PRACTICES
Additional practices or products that a producer may offer as purchaser options:
- Topical concrete sealant. Apply a silane, siloxane or agriculturally based soy methyl ester polystyrene coating in accordance with manufacturers requirements on tread, rise and platform surfaces.
- Concrete densification admixture. The current marketplace provides admixture innovation with crystalline densifiers, latex-modified concrete or hydrophobic additives in different ways to further reduce water and chemical intrusion into the concrete and resistance to scaling. Suppliers of many of these products can be found on the NPCA website. (Precast.org/find)
- Internal heating elements. Precast concrete steps contain a hollow space that some precast step producers provide retrofitting stock inventory steps with electrical heating elements that are placed against the inside surfaces of the step tread and platform to radiate heat and melt the snow and ice. Alternatively, some precasters offer special step fabrication by casting the heating elements directly into the foot traffic areas during the pouring operation. Advertisement claims of snow and ice-free steps in three to five hours upon activation with minimal electrical expense per storm event.