Precast concrete and the ABC technique pave the way for a successful interstate bridge widening in western Pennsylvania.
The nation’s vast network of bridges has faithfully served drivers and pedestrians for decades, but time has taken its toll on many of these structures. With the average bridge now 42 years old and climbing, it stands to reason that more attention is now given to replacing, repairing and rehabilitating these critical structures.
It will be no small feat. According to the National Bridge inventory, there are more than 480,000 bridges serving U.S. highways. The Federal Highway Administration (FHWA) considers 160,000 of those structures to be substandard. And, even as the bridges are rehabbed and removed from that list, roughly 3,000 more are added every year.
“In the coming decades, new bridges will replace many of these spans,” the FHWA said, “but in the meantime, bridge owners need cost-efficient ways to maintain and preserve the existing bridges until they are rebuilt.” 1
The Pennsylvania Department of Transportation (PennDOT) takes this responsibility very seriously and has put a number of bridge repair and rehabilitation projects on its “to do” list over the past few years. Through its $899 million Rapid Bridge Replacement (RBR) project, for example, the agency currently is replacing 558 structurally-deficient bridges statewide.
Precast concrete offers a fast, efficient way to get these and other bridge structures back into tip-top shape. Compared to onsite concrete pours that required lengthy road closures and traffic headaches, precast beams, girders, panels and other products can be manufactured offsite in a controlled environment. This not only ensures consistent quality, but it also minimizes installation time and gets the roadway back into commission faster.
These are just some of the reasons why precast concrete was selected as the material of choice for PennDOT’s recent Interstate 376 Westbound Bridge project. PennDOT administered the project for Almono Partners LP, a regional industrial development corporation. Almono is a partnership of southwestern Pennsylvania foundations that share a vision of a sustainable riverfront community at the Hazelwood Green site (the former LTV Coke Works) in Pittsburgh.
Almono conducted a traffic study and, based on the results, decided that the I-376 bridge over Bates Street needed to be widened. That section of the interstate carries a large volume of traffic in and out of downtown Pittsburgh. The project’s engineer of record, SAI Consulting Engineers of Pittsburgh, immediately began exploring accelerated bridge construction (ABC) options that would both decrease construction time and minimize traffic impacts.
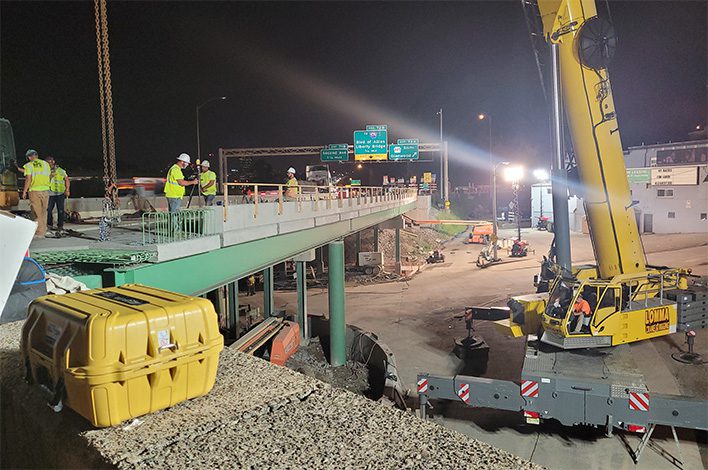
Making the Grade
Project manager Jason M. DeFlitch, P.E., said precast concrete rose to the top of the ABC list fairly quickly. He says SAI completed the design from preliminary engineering stages through construction and that the company did explore a “few other options” before selecting precast. One option was self-propelled modular transport, which would involve building the bridge near the actual bridge site, transporting it and putting it into place.
That option simply wasn’t feasible on this particular project site. The unique constraints of the structure included an adjacent tunnel, multiple ramps and a nearby community that made the self-propelled option infeasible.
“The only means of access to that community is right beside one of the structure’s abutments,” DeFlitch said. “There’s also a historic trail close by, so we had to find a way to construct the wider bridge with a minimal number of impacts — not only to the interstate structure but also to everything situated underneath the highway.”
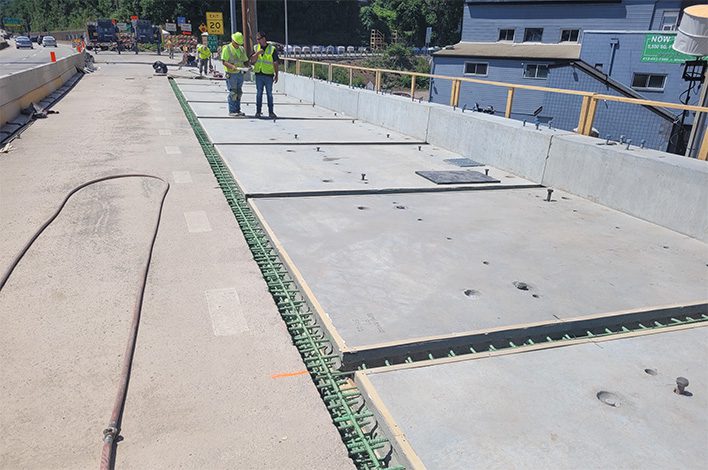
Leveraging ABC in a New Way
The I-376 Westbound Bridge widening introduced some new challenges for the companies that would come together to make the project a reality. For example, an existing bridge had to be widened using ABC bridge construction techniques that are generally reserved for full structure reconstructions. By definition, ABC uses innovative planning, design, materials and construction methods in a safe and cost-effective manner to reduce the onsite construction time that occurs when building new bridges or replacing and rehabilitating existing bridges.
“We then looked into a few different options, but then quickly settled on using a new steel girder line that would allow us to widen the structure and [install] precast deck panels on top of it,” DeFlitch said.
From the engineering perspective, DeFlitch said there also were concerns about the very tight tolerances on this particular project and whether precast pieces constructed in a plant would “meet up” the right way with the existing structure out in the field. With some extra planning, designers were able to eliminate that potential challenge.
“We were able to detail ultra-high performance concrete (UHPC) joints in such a way that would leave flexibility in the field to allow field staff to manipulate the precast deck panels and meet them up with the existing structure,” DeFlitch said. “Then, the contractor brought the two structures together at that point using UHPC joints.”
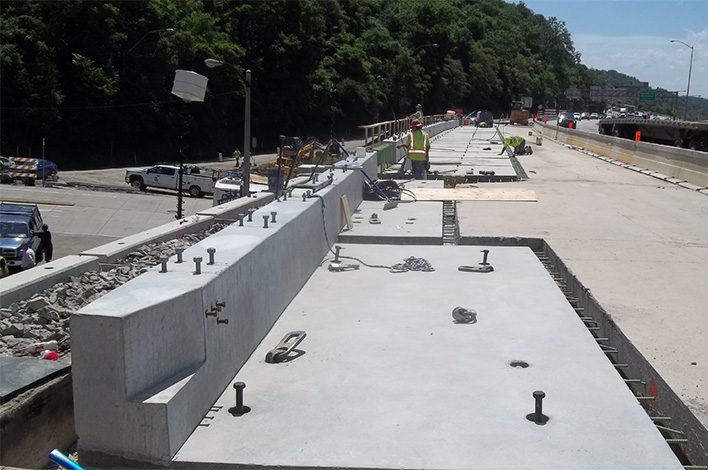
Balancing Time Schedules with Safety Considerations
When setting the bridge rehabilitation project timeline, SAI allocated 15 days for the road closure. DeFlitch said the goal was to take the “minimum amount of time” that PennDOT could reasonably close the interstate down at that point while still safely constructing the new structure.
To keep that closure time to a minimum, much of the foundation work was done in advance. Many of the abutments and piers were widened; foundations were placed (including precast foundations) ahead of time using weekend closures or isolated closures.
“Those short-term closures allowed those components to be widened/worked on ahead of time,” DeFlitch said. “That way, we’d decrease the amount of time that we would need whenever we went to the official interstate closure.”
The precast structures were made by NPCA member Brayman Precast of Saxonburg, Pa., and installed by Allison Park Contractors of Gibsonia, Pa. Brayman works often with PennDOT and was awarded the project through the usual bidding process, according to Dean Kemper, senior project manager. He said the project was pretty much “business as usual” for the precaster, which built the bridge deck, lagging walls and abutment pieces.
Kemper said the existing structure was in major need of repair, with “large chunks of concrete” missing from it. He said the 15-day timeline created some unique constraints, but nothing that the experienced precaster couldn’t work through. He estimated that a cast-in-place structure would have added about 30 days to the construction timeline (for a total of 45 days) and created additional traffic/road closure headaches.
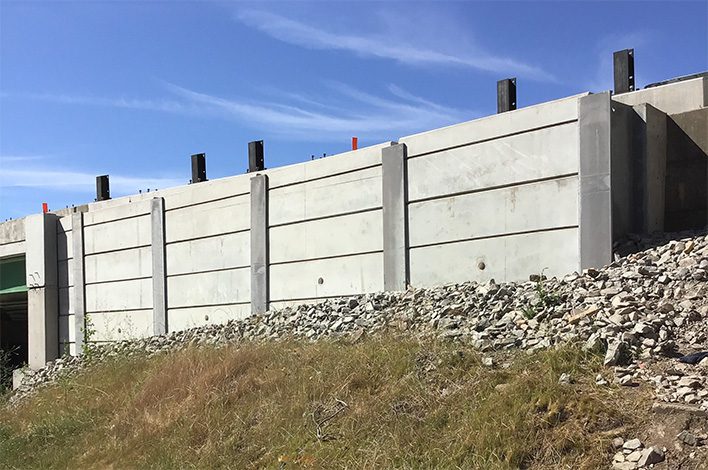
Concrete Results
DeFlitch understands that unexpected surprises can pop up at any time when making old structures new again. This particular project didn’t disappoint on that level, but he said the early planning paid off once the new precast pieces were out in the field and ready to install.
“When you’re doing a rehabilitation project like this one and working with an existing structure, you’re going to come across unknowns in the field,” DeFlitch said. “By putting those UHPC joints in place, we were able to make those adjustments and successfully fit the structure together.”
In the end, the project was completed within the designated timeframe and motorists were back to using the bridge quickly. The owner was pleased with the result.
“The bridge opened on time and PennDOT was happy with it,” DeFlitch said. “The process went smoothly and safely, with zero traffic or construction issues.