StormPrism EQ product uses precast concrete to create an innovative system.
Nestled between the Sierra Pelona Mountains and Castaic Lake, the 430-acre upscale, master-planned neighborhood of Williams Ranch is under construction. Many of the 497 homes, on lots up to 23,000 square feet, will reside inside a gated entry. Homeowners will enjoy built-in advanced technology, a clubhouse and a plethora of popular amenities as well as spectacular mountain views, on-site vineyards, citrus orchards, several pocket parks and an adjoining county park.
When a homeowner purchases a home in a new swanky master-planned development, they expect everything, especially the things they can’t see, to work as planned. That includes the underground stormwater detention system.
Creating a drainage design to serve the Williams Ranch neighborhood development was a challenge for several reasons. California’s stringent stormwater regulations and the Environmental Protection Agency’s Low Impact Development (LID), which calls for site design of new residential developments to focus on reducing pollutant loads, compounded the challenge. Finally, the project was near the Santa Clarita River, an impaired waterway. This required the plan to address the water quality as well as stormwater control.
Analysis was conducted to determine the impact of altering the flow of water throughout the area. The results showed that, to meet LID requirements, both the water flow and volume would need to be reduced.
PRECAST PREVAILS
Initially, the developer, Williams Homes, specified large-diameter corrugated metal pipe (CMP), the most common material used for underground detention systems, for all three stormwater detention systems. The Los Angeles County Department of Public Works (LACDPW), which is responsible for maintenance of the largest stormwater storage system, located underneath the county park, objected to the use of CMP. A CMP stormwater system would require more maintenance and expense than the LACDPW was willing to provide. In addition, the LACDPW also wanted a stormwater system that was durable and safely accessible.
Precast concrete and StormPrism EQ, a modular, precast stormwater system developed and manufactured by Pre-Con Products in California’s Simi Valley, ticked all these boxes and more.
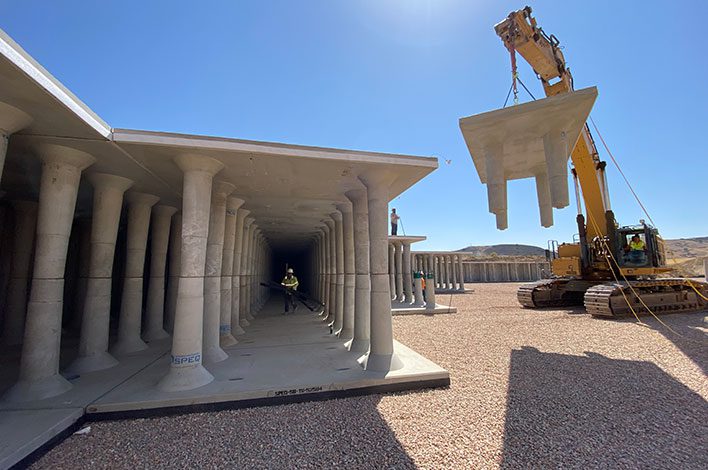
UNIQUE DESIGN
For more than 60 years, Pre-Con, a family-owned business, has provided custom precast solutions for many challenging projects, including proprietary stormwater tanks. Four years ago, it designed the innovative, modular StormPrism underground stormwater storage system.
StormPrism boasts unique features that set it apart from other stormwater systems, such as an open-air design with floor-to-ceiling columns and flat floors.
“All these designs are potential confined spaces, which could make it very difficult and dangerous to move around when performing maintenance inside the structure,” said David Zarraonandia, president of Pre-Con Products.
The unique open-air design and flat, unobstructed floors allow easy movement and visibility for more than 300 feet in any direction, even diagonally. This ensures a clear, unobstructed pathway to the exit is always in view and easily accessible. With StormPrism stomwater detention systems, there’s nothing to block air flow and no restrictions to impede the removal of sediment through the system. The flat floor eliminates trip hazards and improves ease of movement during maintenance.
In October 2023, Pre-Con assigned its StormPrism patents and trademarks to Foley Products.
eadquartered in Newnan, Ga., Foley Products is a leading manufacturer of concrete pipe and precast products, with 18 manufacturing locations in high-growth markets across the United States. Pre-Con continues to manufacture and sell StormPrism products in California and to partner with Foley Products on product development and marketing of the product line.
“Before we acquired the patents, we had been licensing StormPrism for a few years and thought it was an excellent product,” said Anya Civitella, senior vice president of growth and performance for Foley Products. “The addition of StormPrism to our product portfolio is an important step in Foley’s growth strategy. We will now be able to offer high-value stormwater solutions across North America and play an expanded role in the management of one of society’s most vital resources.”
The company anticipates a growing need for drainage infrastructure due to the increase of intense storm systems in many parts of the country. These strong storms have the potential to overburden and eventually overwhelm our current infrastructure system.
“StormPrism was designed with openness, maintainability and safety in mind, which mitigates many issues that other products have had over the years. It is also very easy to install,” said Scott Hensley, vice president of stormwater for Foley, who previously worked for Oldcastle Stormwater Solutions and Contech Engineered Solutions. “In other words, it is the next generation of underground detention systems.”
FABRICATING THE MODULES
For the Williams Ranch project, Pre-Con fabricated a stacked system of 800 modules – 400 top pieces and 400 bottom pieces – that formed the interior of the underground detention system and 120 walls that surround its perimeter. Each module is approximately 8 feet by 16 feet, with an interior height of 11 feet, and weighs less than 20,000 pounds. Generally, the walls measure 8 feet wide by 12 feet 4 inches tall by 12 inches thick.
Pre-Con poured concrete with a compressive strength of 6,000 psi into steel molds to create the precast pieces. Pre-Con’s facility is a National Precast Concrete Association Certified Plant.
The company also created a fabric-covered basket for the system to filter the fine sediment in the stormwater before it is released. Sediment in an infiltration storage system can weaken its effectiveness.
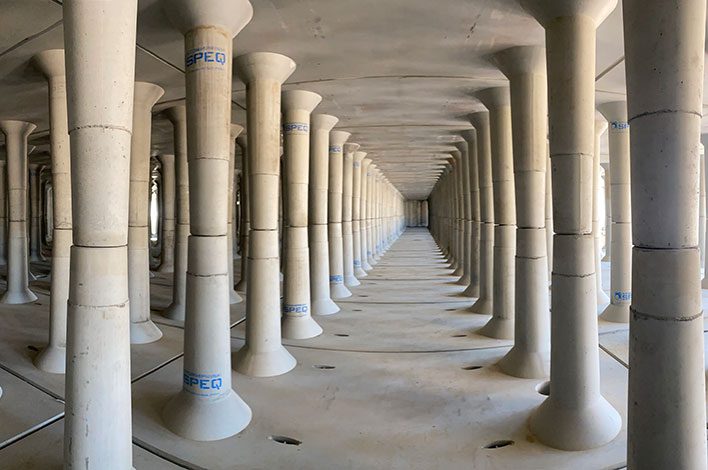
QUICK AND EASY INSTALLATION
The project was completed in three phases. Pre-Con installed the system with the help of R&R Pipeline, who supplied extra labor and additional equipment. Pre-Con began shipping precast elements to the job site, which was about 35 miles away, on Aug. 24, 2021. The modules shipped via a standard load semi-truck – typically two pieces per truckload. The staging area was large enough that the precast modules and walls could be stockpiled on-site until enough stock was accumulated to complete a phase. Then they would be installed, and the process would begin again.
The modules fit together via the tongue and groove method. Since the modules are identical, installation is nearly foolproof.
“There were no problems with the project,” Zarraonandia said, “but there were certainly a number of challenges.”
One challenge was that the project took place during the COVID pandemic. Pre-Con had to deal with workers becoming ill and off the job for weeks and the restrictions imposed during the COVID years.
But the main challenge involved the sheer size of the system. The footprint created by the modules and walls measures 164 feet by 324 feet. The excavation itself was more than 300 feet long by 200 feet wide. Pre-Con’s access point was a steep road 25 feet above the rock bedding material, and access was available from only one side. A crane would have had to pick a module from more than 300 feet away. That was not an option.
The solution: Pre-Con used a large excavator to access the excavation.
“Because of the nature of our design and the shape of our pieces, we were able to pick the modules up with a forklift or a fork attachment on the front of a loader,” Zarraonandia said. “Not only did we find a way around it, our productivity for placing the modules was far better with the excavator than we ever experienced using a crane.”
It’s the speed at which the system was installed that makes this project stand out. Workers installed the modules at a rate of nearly 70 per day. The first phase was installed on Sept. 3, 2021, and all three phases were completed by mid-November.
“We’re receiving a lot of positive feedback from many of the engineers we deal with,” Zarraonandia said, “specifically when it comes to the simplicity of the design, the ease of installation and the maintainability of the system compared to some of the other systems out there.”