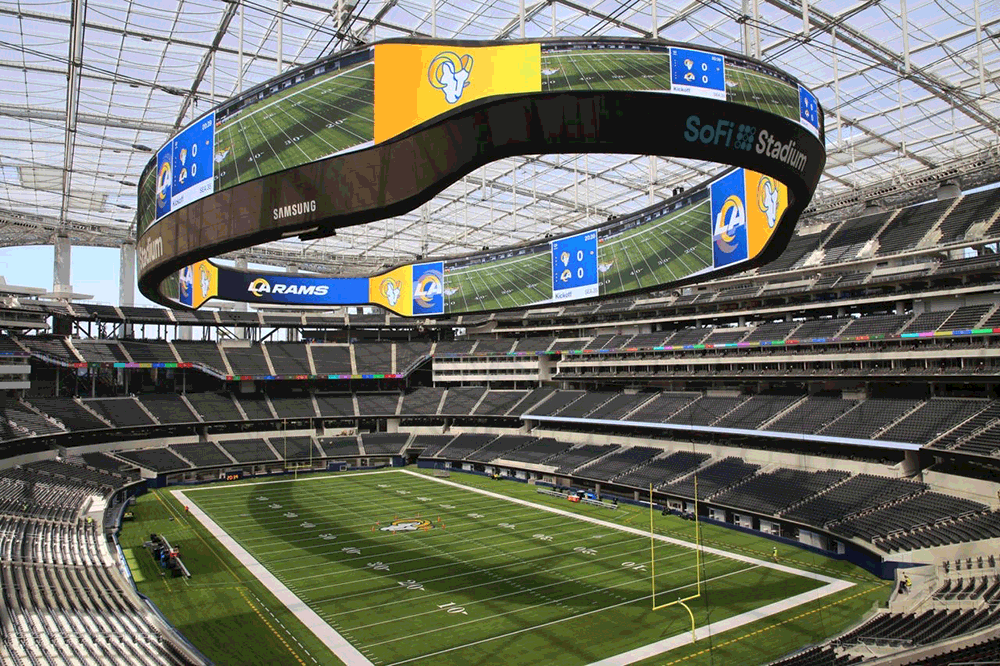
Millions of football fans worldwide will tune in Sunday to watch the Cincinnati Bengals and Los Angeles Rams play for the NFL title in Super Bowl LVI.
Eyes will gravitate to the action on the field, but the green grass and white lines are just the final touches on what was a $5 billion project to build SoFi Stadium.
INFOGRAPHIC: SoFi Stadium – By The Numbers
In order to prepare for an NFL schedule and to serve as the home for two franchises beginning with the 2020 season, the stadium underwent four years of massive construction to transform it into a state-of-the-art facility featuring the latest technology and expanded capacity.
Three NPCA members – Euclid Chemical, Olson Precast Company and Delta – played big roles in the construction and now have an international audience for which they can show off their hard work for decades.
The 3.1-million-square-foot facility also is slated to host a variety of iconic events beyond this week’s big game, including the College Football Playoff Championship in 2023 and the Opening and Closing Ceremonies of the 2028 Olympic Games.
Euclid Chemical
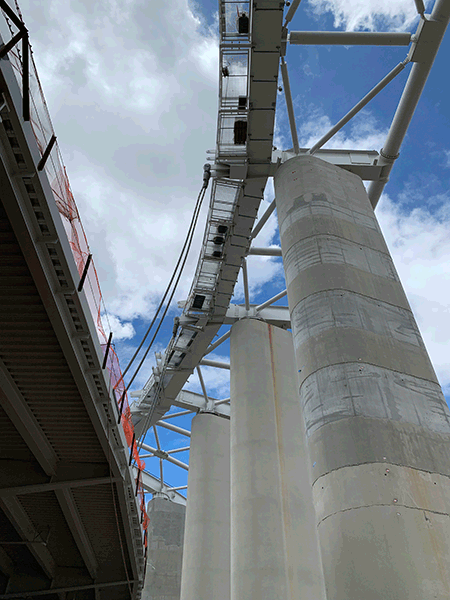
After breaking ground in November 2016, Euclid Chemical’s TUF-STRAND™ SF polypropylene/polyethylene macro-fiber product was added at a dosage rate of 5 lb/yd³ (3 kg/m³), serving as a synthetic structural fiber reinforcement for the topping slabs of the stadium’s upper-level decks. By substituting conventional reinforcing with structural macro-fibers, this improved crack control and reduced corrosion potential for the topping slabs.
As a result, Euclid’s TUF-STRAND SF synthetic macro-fibers significantly reduced construction costs by eliminating the time and labor needed to install conventional steel or welded wire mesh reinforcing.
“This is another exciting example of a successful project where macro-fibers have been used as a viable alternative to conventional reinforcement – resulting in reduced construction costs, less environmental site impact, improved worker safety and the ability for the contractor to place more concrete faster with less manpower required,” said Mike Mahoney, director of marketing and technology for fiber-reinforced concrete at the Cleveland-based Euclid Chemical. “We are looking forward to seeing more projects like SoFi Stadium constructed with Euclid fibers in the future.”
Olson Precast Company
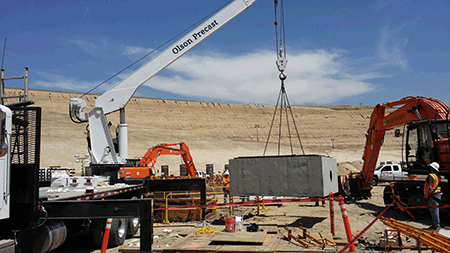
Olson Precast’s Rialto, Calif., facility laid the early infrastructure upon which SoFi Stadium stands.
Olson constructed and installed a 120-inch sewage pump station, four 96-inch sewage pump stations, two 6-foot-by-6-foot sewage ejector vaults and four 8-foot-by-8-foot sewage ejector vaults – all at about 20 feet deep.
“We worked on a lot of things that are underneath everything,” said Matt Johnson, the quality control manager at Olson’s Rialto plant. “First, they dig a big hole, then we do our work, then everyone else does their work on top of that. You won’t see any of our work first-hand, but that’s OK. We know it’s there, and it’s an important part to the success of any stadium.”
Delta
Delta was contracted to design the 45-foot-tall goal posts along with the anchorage to the foundation and the concrete drilled shaft foundations.
“It’s not often we get to see our work,” Delta Project Manager Kristy Vander Werff said. “We are looking forward to seeing one of our projects on national television during the Super Bowl.”
Joe Frollo is director of communications and public affairs at NPCA.
Leave a Reply