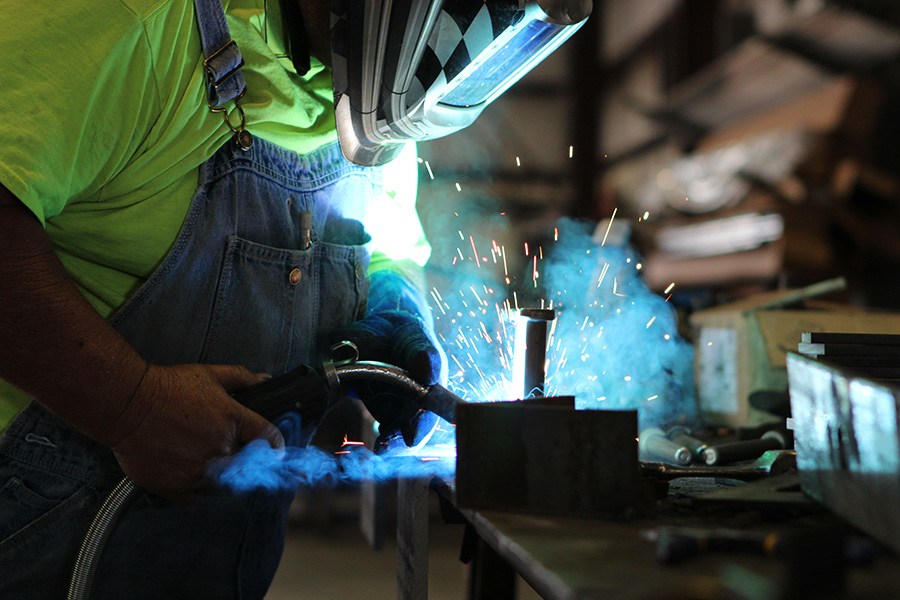
Master the art of welding rebar at your precast plant.
Precast concrete is a versatile product that offers quick and efficient installation, which reduces a contractor’s time in the field. This is one of the biggest selling points of precast products. Though we preach this to our customers, contractors and specifiers, there are still many precast producers who do not practice what they preach in their own plants. Specifically, I am referring to the production and installation of prefabricated rebar reinforcing mats and cages.
Many plants still tie and build their rebar cages around forms. While there may be some instances where there is no other option, producers can often save production time by prefabricating rebar reinforcement. A common remark from precasters is,
“Wire ties will not provide a rigid or strong enough connection to keep the cage in tolerance or even hold together during transportation of the reinforcing cage to the form.”
The solution is welded rebar reinforcement. Welding rebar cages and mats allows them to be easily transported – without worry – to the yard or into forms. The welds provide a rigid and structural connection that will keep the bars in their correct locations during movement, form setup, pouring and vibrating.
For many, welding rebar has been deemed unacceptable or difficult to do. However, it is just the opposite. It is acceptable and practical as long as certain standards and practices are followed. These standards and practices include:
- Selecting the correct rebar
- Determining and performing the proper preheat, if needed
- Selecting the correct filler (welding rod or wire)
- Selecting proper weld, metal preparation and placement
Select the correct rebar
ASTM A615 rebar
The first important step is the selection of the proper rebar for your application. The most common rebar used in concrete reinforcing is produced in accordance with ASTM A615/615M, “Standard Specification for Deformed and Plain Carbon-Steel Bars for Concrete Reinforcement.” This rebar’s chemical makeup and physical properties vary from structural steel. Rebar is typically less ductile with a higher tensile strength.
These properties are a result of the chemical makeup of the rebar, in particular the carbon content. Higher carbon content adds difficulty to making a sound weld, and is typically the reason offered for not welding rebar. The National Precast Concrete Association Quality Control Manual for Precast Concrete Plants states in Section 4.2.2, “Welding of ASTM A615 reinforcing steel is not generally an acceptable practice.” However, if the carbon equivalency (C.E.) for A615 steel is calculated to be .55% or less for rebar sizes up to #6, and less than .45% for bars larger than #7, the rebar can be welded with no preheating. This specification is found in American Welding Society D1.4/D1.4M, “Structural Welding Code-Reinforcing Steel.” The carbon equivalency can be calculated by using the equation:
C.E. = %C+%Mn/6
The percentages of the carbon and manganese can be found in the mill certificates provided with your rebar shipment.
ASTM A706 rebar
Another option is rebar manufactured to meet ASTM A706/706M, “Standard Specification for Deformed and Plain Low-Alloy Steel Bars for Concrete Reinforcement.” This rebar can be differentiated from A615 bar by the “W” found stamped on the bar. This rebar is considered weldable and is required to have a carbon content of .55% or less. Therefore, the carbon equivalency is not required to be calculated. However, it is advisable to perform the calculation to verify the rebar supplied meets the carbon requirements. You will also want to perform the calculation if you are using rebar larger than #6 because carbon equivalency will dictate the preheat temperature required, if needed. To calculate the carbon equivalency of ASTM A706 rebar, you must use the equation:
C.E. = %C+%Mn/6 + %Cu/40 + %Ni/20 + %Cr/10 – %Mo/50 – %V/10
Again, all of these percentages are found in the rebar mill certificate.
Determine the preheat temperature
Once the carbon equivalency has been calculated, Table 5.2 of AWS D1.4 should be referenced to determine if preheating is needed for the rebar. Table 5.2 provides the minimum temperature required to preheat the rebar prior to welding. For most rebar that can be welded under the carbon equivalency, there is no preheat temperature required. If the C.E. value is higher or a larger diameter rebar is used, the preheat temperature for the rebar may be anywhere from 100 to 500 degrees Fahrenheit. For typical precast reinforcing, it is uncommon for rebar to require a preheat in excess of 100 F. If it is determined that your rebar requires a preheat temperature minimum, the rebar to be welded must be brought up to the minimum temperature stated. In the case that different pieces of rebar are welded together, both must be brought to the minimum preheat required by the bar with the highest preheat temperature. For instance, if you are welding a #5 rebar that requires no preheat to a #6 rebar that requires 100 F preheat, both bars must be preheated to a minimum of 100 F.
One final consideration is cold-weather welding. If you stockpile your rebar outside and the temperature is less than 32 F, all rebar (regardless of C.E.) must be brought to 70 F prior to and during welding.
Select the correct filler
Another important factor that must be considered is the method of welding and type of filler metal. Under AWS D1.4, there are three options available for welding rebar. These are Shielded Metal Arc Welding (SMAW, commonly called arc or stick welding), Gas Metal Arc Welding (GMAW, commonly called MIG or wire feed) and Flux Core Arc Welding (FCAW, wire feed with flux-coated wire in place of gas).
Table 5.1 in AWS D1.4 provides the requirements for filler metal needed to weld the rebar. An example would be the method for A615 grade 60 rebar. If the method of welding was SMAW, an electrode of E9015-X, E9016-X, E9018-X or E9018M would be used. If using the GMAW method, an electrode of ER90S-XXX or E90C-XXX would be required. If two different bar grades or specifications are welded together, the electrode for the rebar with the higher tensile strength is used. For example, if an A706 grade 60 bar is welded to a A615 grade 60 bar, the electrodes required for the A615 grade 60 are used. This is because the tensile strength of the A615 rebar is 90,000 psi while the A706 rebar is only 80,000 psi.
In addition to the preheat and filler requirements listed in AWS D1.4, there is also a section illustrating the allowable types of joint welds. These include butt joints, lap joints and splices. However, under AWS D1.4 there is no provision for bars crossing at 90 degrees to each other. For mats or cages requiring welding bars that cross perpendicular to each other, ASTM A184/A184M, “Standard Specification for Welded Deformed Steel Bar Mats for Concrete Reinforcement,” provides guidance and should be considered the standard. Under this specification, the producer must ensure that all bars are “substantially parallel and perpendicular to each other.” The standard requires all joints around the perimeter of the mat or cage be welded, but only every other bar for interior intersections.
Once all the requirements for preheat, electrodes and welds have been established, the reinforcement can be welded. For reinforcing that goes in a stock product, it is a good idea to build a jig to speed up production and ensure the bars are in the correct location at all times during the fabrication of the reinforcing cage or mat. In the absence of a dedicated fixture, other items such as clamps and vise grips are recommended to keep bars in their correct location. It is important to take time in this step. If a mistake is made or a bar moves during welding and is determined to be out of tolerance, it must be cut and repositioned. Depending on the severity of the cut, additional splicing or an entire bar replacement may be needed. When preparing reinforcement, ensure it is free of dirt, mud, water, snow, flaking or pitting rust and form oil prior to welding. These items will prevent a thorough weld and will negatively affect the concrete-to-rebar bond. Minor surface rusting that has not pitted or damaged the bar will not create any issues and is typically acceptable. After the welding has been finished, make sure to chip and remove any slag that is on the welds. This is typical of SMAW and FCAW welds. Inspect to confirm the welds are of sufficient size and provide uniform penetration into both bars. Once you are finished, allow the welds to cool naturally. Never accelerate cooling, as this will likely negatively affect the structure of the bars. At this point, the rebar cage or mat is ready to stockpile until time of use.
Making better precast
Welding rebar cages may seem like a daunting procedure with many standards to adhere to; however, it is actually a fairly simple process. The preparation time calculating carbon equivalency and determining correct preheat, rebar and filler is very minimal. These steps boil down to a few minutes that can be performed by a quality control technician or other trained individual at the time the rebar is received. Plants can help streamline the process by selecting a single class of electrode that covers the majority of rebar varieties used. In addition, purchasing ASTM A706 rebar ensures that it is always at or below .55% carbon equivalency. Rebar chairs and/or wheels can be installed ahead of time as well to save a few minutes when installing the cage into the form. This all adds up to a higher quality, more efficient and safer precast product due to the precise and secure placement of the rebar.
Andrew Hayward, P.E., is the production and quality control manager at Panhandle Concrete Products in Scottsbluff, Neb.