Editor’s Note: This is a modified version of an article that originally appeared on Builder’s website (1).
I decided to take a hard look at a compelling option most commonly used for basements, but also well-suited for above-grade walls – engineered precast concrete. With this technology, off-site production facilities pour concrete into forms configured to detailed construction plans.
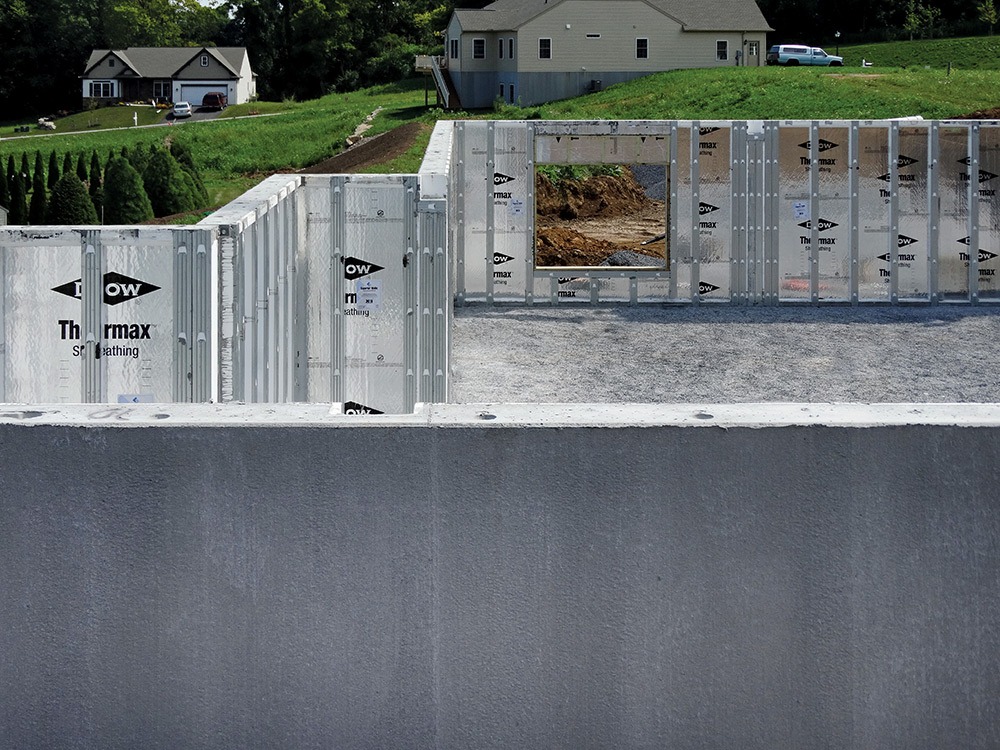
One of the most popular manufacturers for residential construction of this type is Superior Walls. Their forms result in a concrete wall configuration that includes a thin profile top bond beam, less than 2-inch-thick exterior skin and ribs two feet on center. Extruded polystyrene rigid insulation is bonded to the panels between the ribs, and the top bond beam and ribs are faced with 1 inch of expanded polystyrene. Thus, the system effectively includes a complete thermal break. Additional insulation can be installed in the space between the ribs for a higher R-value, where desired. The front edge of the expanded polystyrene ribs is faced with galvanized metal studs for directly installing a finished wall and the ribs are pre-drilled for wiring and plumbing. The total wall thickness is 10 1/4 inch.
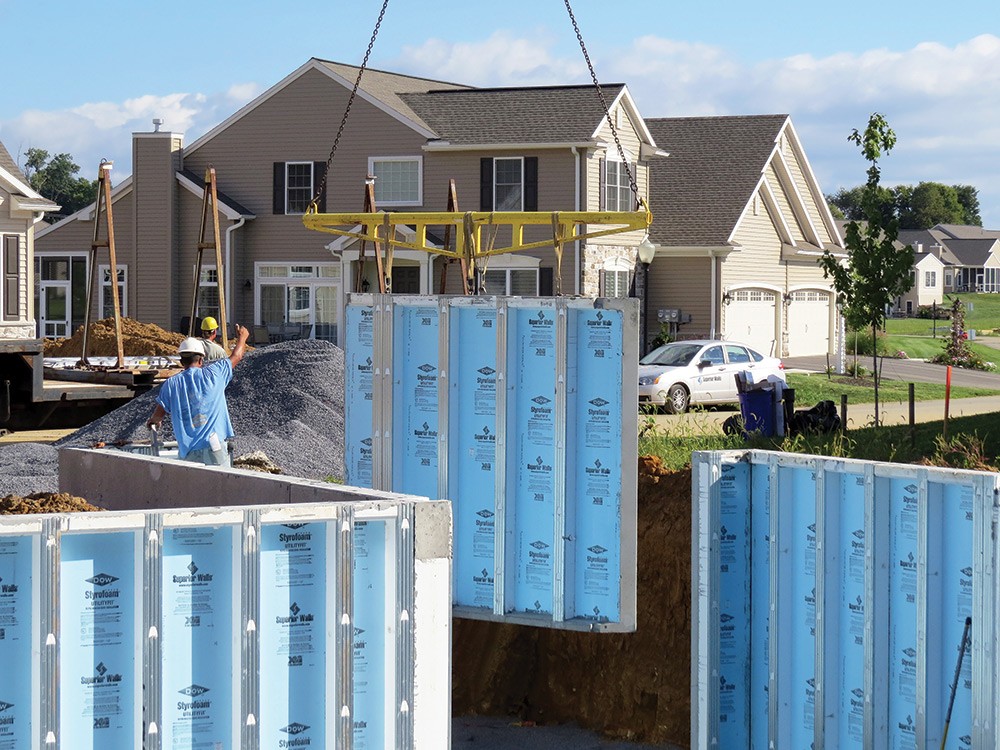
Completed wall panels are installed in the field with cranes directly on a gravel bed without the need for a footing. Once installed, the panels are effectively bonded together for greater strength than a conventional concrete foundation, even though the system is so resource-efficient it can use up to 75% less concrete than a conventional foundation. A typical precast foundation can be installed in one day.
Precast’s many advantages
Concrete represents a complete platform change from traditional wood framing. This is significant because as a construction material, wood burns incredibly easily, rots when wet, serves as food for insects, has poor dimensional stability, offers minimal impact resistance and provides no thermal storage capacity. In contrast, concrete is noncombustible, moisture-resistant, insect-resistant, impact-resistant, dimensionally stable and has excellent thermal storage capabilities. However, one key challenge with precast wall systems is that on-site workers must be skilled and held accountable for perfectly level grades. Consider the following impressive benefits:
Construction
- Faster construction time
- Fewer tools for assembly
- Substantially reduced subcontractor work (such as integrated framing, chases, insulation, air sealing)
- Substantially less waste
- Superior dimensional accuracy helps ensure better quality fit, finish and trim
- Smaller heating and cooling systems due to substantially reduced loads and outstanding control of mean radiant temperatures
- Year-round construction, since precast concrete can be installed in cold weather
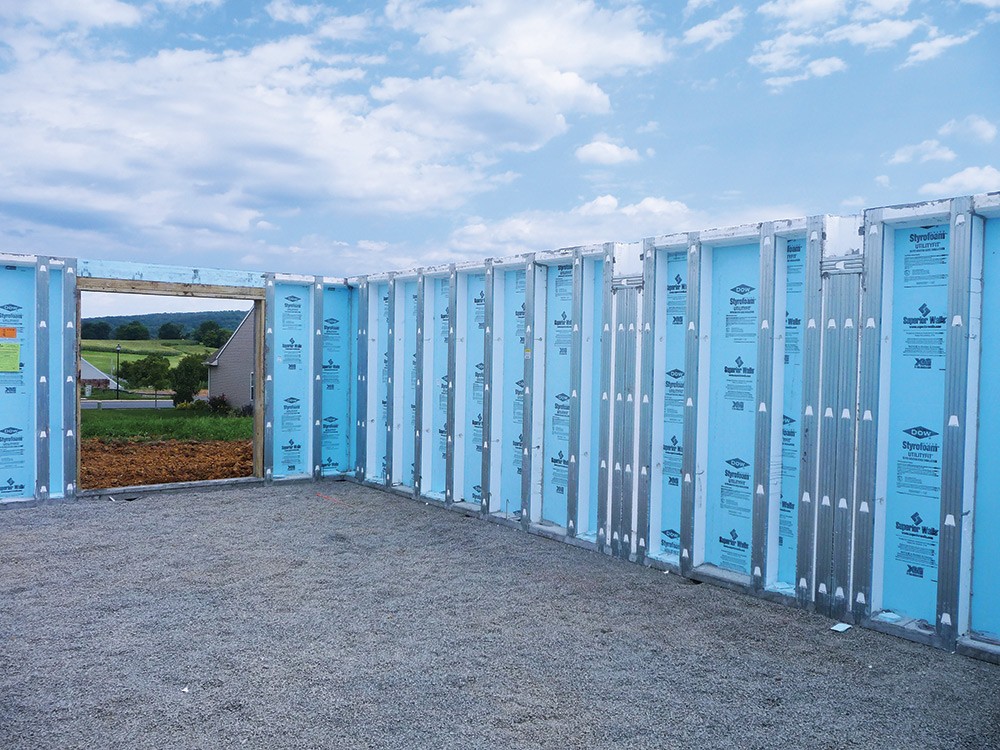
Performance
- Strength (effective bond beam results in added strength)
- Disaster-resistance: impact, water, wind and fire
- Moisture protection (5,000-psi precast concrete is nearly waterproof compared to more porous 2,500-psi concrete used in conventional foundations)
- Drainage (the absence of a footing provides a clear path for sub-slab moisture to the foundation drain)
- Sound mitigation
- Energy performance: minimal thermal bridging, insulation installation quality (no gaps, voids, compression) and an inherently airtight assembly
- Moisture storage to buffer the home from moisture-related issues
- Resource efficiency requiring substantially less concrete for foundation
- Space savings (finished basements with conventional foundations also need a framed assembly and air space that can add approximately 6 inches around the perimeter, consuming about 80 square feet of space in a 1,500-square-foot plan)
I’m interested in the possibility of also using precast panels for the slab, with the flat exterior skin facing the ground. I understand this would have to be engineered for necessary lateral support, but this innovation would add impressive benefits. First, it would eliminate virtually all limitations for winter construction by allowing all foundation work – walls and floor – to be installed in cold temperatures. Second, it would eliminate the complications and labor associated with installing rigid insulation under the slab. And most importantly, it would result in a diaphragm floor in the basement, where a typical oriented strand board or other sheathing is fastened to the metal studs covering the ribs. This would enable the basement to feel just like an above-grade floor. In other words, you would be building true lower levels rather than basements. And the gap between the subfloor and rigid insulation could be used as valuable space for wiring and plumbing.
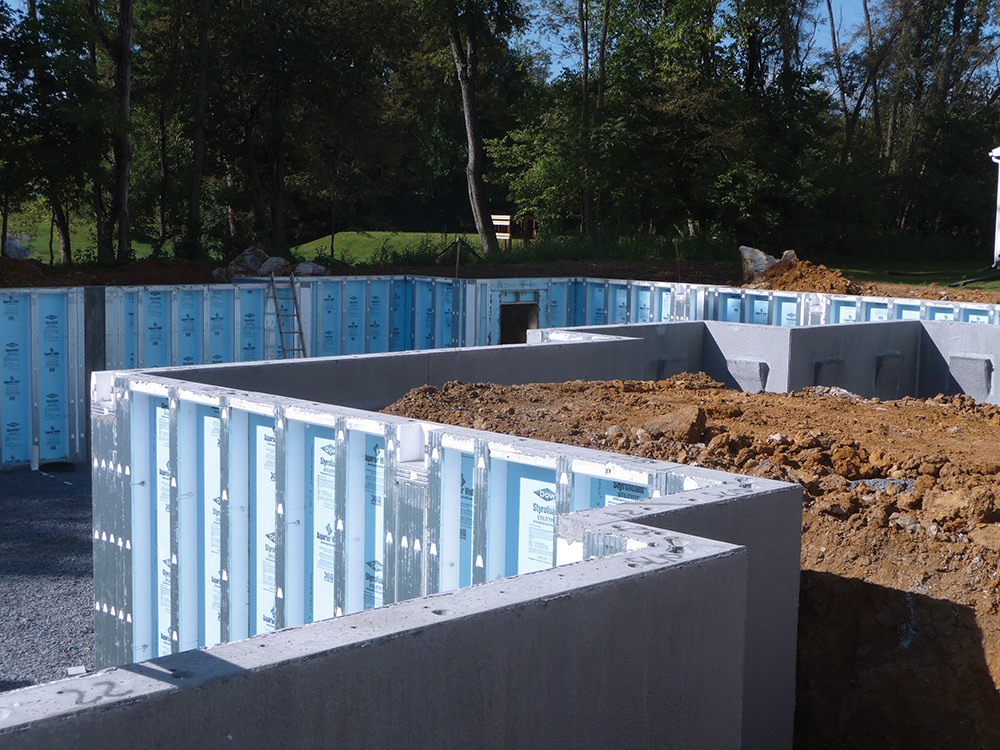
Although this alternative technology offers an impressive list of advantages and has been around a very long time, the market share remains low. But that may be starting to change. Kiere DeGrandchamp, president of High Performance Homes, was convinced to give precast technology a try. He switched in the middle of development to a precast concrete foundation for his homes at The Links at Gettysburg in Gettysburg, Pa. When we discussed his experience following initial installation, he admitted there were some bumps getting past a few learning curve issues, especially since the project entailed a relatively complex design and site. However, he loved the substantially improved results and knows the next endeavor will be significantly easier. He is not turning back.
I am not associated with or financially linked to any product, technology, builder or manufacturer. I’m simply a long-time industry observer asking tough questions regarding why so many compelling new technology solutions – like precast concrete – are so slow to be embraced when they offer so many solutions and benefits to the housing industry.
Sam Rashkin is the chief architect of the Building Technologies Office for the U.S. Department of Energy. He has earned a national reputation for his work leading housing programs that have resulted in more than 1 million certified high-performance homes. He is the author of “Retooling the U.S. Housing Industry: How It Got Here, Why It’s Broken, and How to Fix it.” Learn more about Sam at samrashkin.com.
Endnotes
(1) builderonline.com/building/structure-durability/gray-matter-platform-performance_o