All air voids in concrete are not created equal. Find out the difference between beneficial air entrainment and accidental, or detrimental, air entrapment
In regions where temperatures can frequently fluctuate near freezing, freeze-and-thaw cycles pose one of the greatest challenges to concrete durability. Capillary voids will form during concrete production, so protection against capillary ice damage must be designed into the precast concrete product. Air-entraining admixtures are one part of the solution that will prevent damage from freeze-thaw conditions.
The importance of entrained air was first noticed during the 1930s, when certain highway sections were found to be more immune to the effects of freezing and thawing than others. Studies traced it to cement that was milled at plants using beef tallow as a grinding agent. The beef tallow was an unintended air-entraining agent, and it improved the durability of the concrete.
During hydration, the reaction of water and cement leaves capillary cavities, or voids, that become filled with water when a precast product is exposed to wet conditions. As the capillary water freezes inside concrete, it expands about 9% in volume. The water-to-ice volume change exerts internal pressure inside the concrete that exceeds its tensile strength, causing cracking, spalling and eventual disintegration. Entrained air pockets provide a relief system for internal ice pressure by providing internal voids to accommodate the volume expansion caused by freezing water.
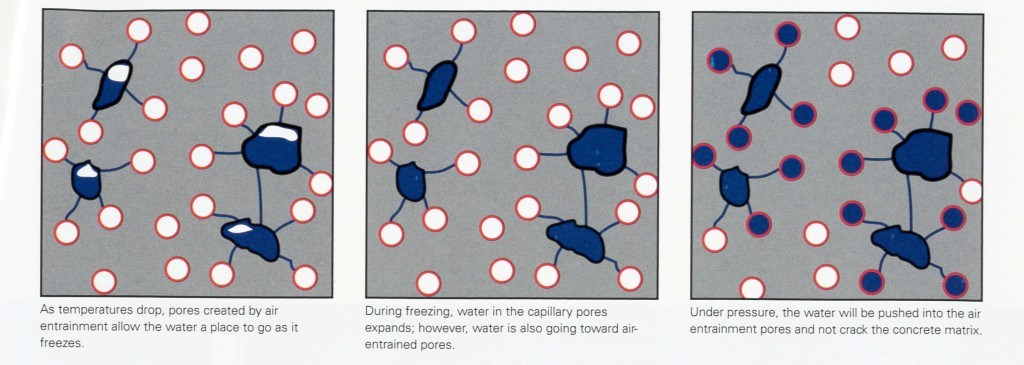
Entrapped air is problematic
It is important to note that entrained air is not the same as entrapped air. Entrapped air is created during improper mixing, consolidating and placement of the concrete. Air pockets, or irregularly sized air voids, are spread throughout the concrete and have negative effects on product appearance, strength and durability. Proper vibration techniques can be helpful in removing entrapped air.
Entrained air is intentionally created by adding a liquid admixture specifically designed for this purpose. The goal is to develop a system of uniformly dispersed air voids throughout the concrete. Proper use of air-entraining admixtures ensures the development of the correct spacing, size (usually measured in micrometers) and amount of these voids. These voids absorb the pressure created by the expansion of the freezing water.
Spacing and size of entrained air make a difference
The criterion for spacing is defined as the maximum distance the water would have to move during freezing before reaching the safety valve, or capillary void, of an air reservoir. This recommended average “spacing factor” should not be greater than 0.008 in., according to ASTM C457, “Standard Test Method for Microscopical Determination of Parameters of the Air-Void System in Hardened Concrete.”
The size of these voids is also important. The “specific surface” is the average surface area of the voids in hardened concrete per unit volume of air. The specific surface necessary for adequate resistance to repeated freezing-and-thawing cycles is recommended to be greater than 600 sq in./cu in.
One of the concerns with air-entraining admixtures is that they can decrease the strength of the concrete. Typically, an increase of 1% in air content will decrease concrete’s compressive strength by approximately 5%. Therefore, it is important that air content be closely controlled. The NPCA Quality Control Manual for Prestressed and Precast Concrete Plants recommends air content tests be conducted for at least every 150 cu yd of concrete produced and not less than once a day when air entrainment is used. However, state and local specifications may require more frequent tests. The air content test should be conducted in accordance with either ASTM C173-10b, “Standard Test Method for Air Content of Freshly Mixed Concrete by the Volumetric Method,” or C231-10, “Standard Test Method for Air Content of Freshly Mixed Concrete by the Pressure Method.” Note that ASTM C173 requires all samples for acceptance testing be taken from the middle third of the batch.
The recommended air content varies with the severity of exposure and aggregate size. For instance, 3/8-in. aggregate with a severe exposure (frequent freeze-thaw cycles) requires 7.5% air content, while the same aggregate with moderate exposure requires 6% air content. A 1-in. aggregate requires 6% for severe exposure and 4.5% for moderate exposure. Air-entraining agents are generally added to the mix in a range from 0.25 to 2 fl. oz./100 lb. of cementitious materials. This is a broad range, and proper dosage should be determined after consulting the admixture supplier, and considering mix design, materials and trial-batch test results.
Many mechanisms affect air content
Many factors affect entrained-air stability:
• Finer cements with low alkali content
• Fly ash mixtures and an increase in fine aggregates passing the No. 100 sieve
• Dust and very fine material on coarse aggregates
• Hard mixing water (high mineral content)
• Detergents that can add soap bubbles
• Other chemical or mineral admixtures such as water-reducing agents and superplasticizers used in the concrete mix
• Batch size and mixer settings (rotation rates and times)
Every mix component – from cementitious material to aggregates and water, as well as methods used for batching, mixing, placing, consolidating and finishing – can affect the final air content, so production steps must be monitored closely. All these production variables mean that trial batches are necessary to determine the appropriate amount of air entrainment.
What goes into air-entraining admixtures?
Today’s air-entraining admixtures are primarily liquids produced from byproducts (salts) of wood resins. However, there are new products made from synthetic detergents, sulfonated lignins, petroleum acids, proteinaceous materials and sulfonated hydrocarbons. There are also particulate air-entraining admixtures composed of hollow plastic spheres and crushed brick. Although outside the scope of this article, there are air-entraining cements that meet ASTM C150, “Standard Specification for Portland Cement.” These cements have an “A” identifier, such as Type IA or IIIA.
The specifications for air-entraining admixtures are covered in the ASTM C260-10a, “Standard Specification for Air-Entraining Admixtures for Concrete.” This specification sets limits on the impact of the admixture for concrete bleeding, set time, strengths, compressive and flexural strengths, freeze-thaw resistance, and length change during drying. The manufacturer of the admixture should guarantee that its product meets this specification.
Entrained air is one of the critical techniques available to precasters to reduce the impact of freeze-thaw processes and ensure the durability of precast concrete in severe climates. Because so many production variables can affect air entrainment, careful monitoring and trial batch testing are the foundation for proper air entrainment and a long service life for exposed precast concrete products.
By Claude Goguen, P.E., LEED AP is NPCA’s director of Technical Services.